Nachhaltige Fertigung erfordert,
Ressourcen schonend einzusetzen und kontinuierlich zu recyceln.
Die Betonsteinindustrie setzt auf eine nachhaltige Produktion, indem sie regionale Rohstoffe wie Sand, Kies und Naturstein verwendet, die unter hohen Umweltstandards gewonnen werden. Durch kurze Transportwege wird der CO2-Fußabdruck minimiert. Ein hoher Anteil an Recycling-Gesteinskörnung, gewonnen aus Produktionsabfällen und Betonbruch, reduziert den Einsatz von Primärrohstoffen. Innovative Prozesse ermöglichen die Wiederverwendung von Restmaterialien wie Beton, Wasser und Staub, wodurch ein geschlossener Stoffkreislauf entsteht. Zusätzlich tragen CO2-effiziente Zemente und moderne Fertigungstechnologien dazu bei, Emissionen zu senken.
Heimische Rohstoffe
In Deutschland werden die Gesteinskörnungen, wie Sand, Kies und gebrochener Naturstein (Splitt, Schotter) unter hohen Umwelt- und Sozialstandards gewonnen. Die Genehmigungsverfahren für den Rohstoffabbau schließen überwiegend eine Prüfung der Umweltverträglichkeit des Vorhabens sowie eine breite Öffentlichkeitsbeteiligung ein. Somit ist sichergestellt, dass andere öffentliche Interessen beim Rohstoffabbau berücksichtigt werden.
Dem eigentlichen Genehmigungsverfahren sind weiterhin langjährige Prüfungen der Raumverträglichkeit im Rahmen der Landes- und Regionalplanung vorgeschaltet. Ein großer Vorteil bei der Herstellung von Betonsteinprodukten aus heimischen Rohstoffen liegt in der Transparenz der Umweltauswirkung und der Sicherheit, dass die mit dem Eingriff verbundenen Auswirkungen funktional ausgeglichen werden. Die Gewinnung der Rohstoffe erfolgt bedarfsgerecht ohne Überproduktionen. Das schont natürliche Ressourcen.
Kurze Transportwege durch regionale Verfügbarkeit
Auch unter dem Gesichtspunkt der Minimierung des CO2-Fußabdrucks spricht alles für heimische Rohstoffe. Die Steine- und Erden-Industrie, zu der die Betonsteinindustrie gehört, ist dabei hierzulande im Vergleich zu anderen Branchen sehr gut aufgestellt. Den mengenmäßig größten Teil im Beton nehmen die Gesteinskörnungen, wie Sand, Kies und gebrochener Naturstein (Splitt, Schotter), ein. Ihr CO2-Fußabdruck wird unter anderem von der Transportentfernung bestimmt. Nach einer Erhebung des Bundesverbandes Baustoffe – Steine und Erden unter seinen Mitgliedern werden in Deutschland Bausande und Baukiese im Durchschnitt nur rd. 30 Kilometer per Lkw transportiert. Der Transportanteil der Lkw liegt bei 82 Prozent. 18 Prozent teilen sich Bahn und Schiff. Beim Naturstein sieht es ähnlich aus.
Die durchschnittliche Transportentfernung mit dem Lkw liegt bei lediglich 40 Kilometern, bei einem Transportanteil von 94 Prozent. Auch der Transport von Zement und Hüttensand, die heute wichtigsten Bindemittel für die Betonsteinherstellung, erfolgt überwiegend auf regionaler Ebene. Nach der oben genannten Erhebung werden Zement und Hüttensand in Deutschland im Durchschnitt jeweils rd. 100 Kilometer per Lkw transportiert. Zement wird dabei zu 96 Prozent und Hüttensand zu 70 Prozent mit dem Lkw transportiert. Von der Betonsteinindustrie werden somit hauptsächlich regional verfügbare Rohstoffe genutzt.
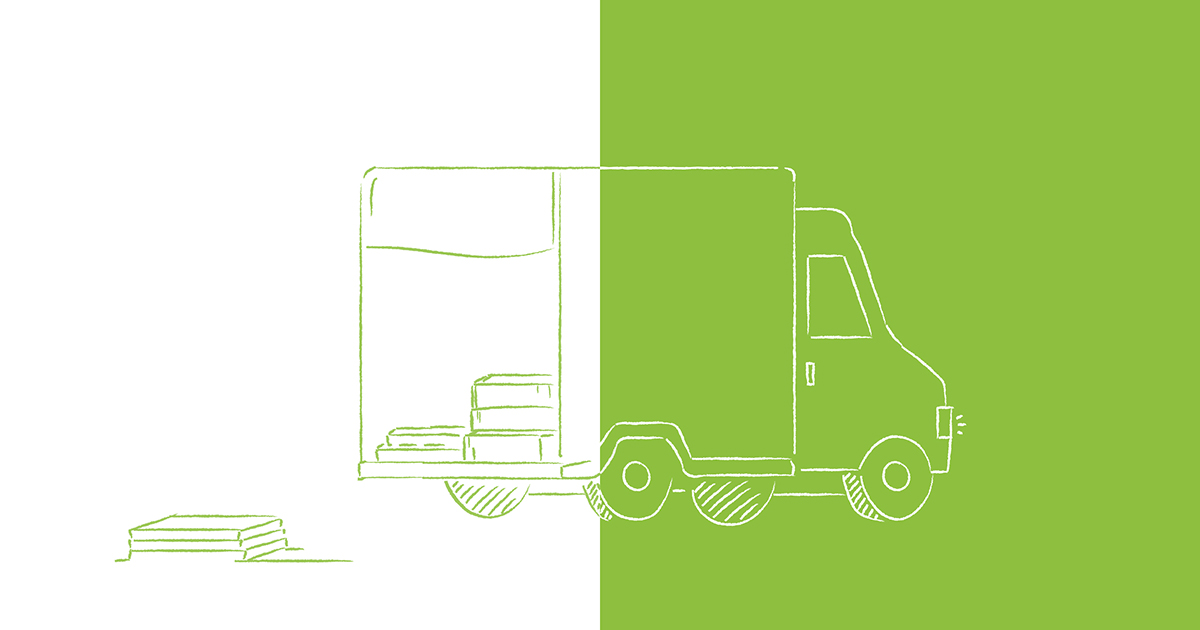

Der schonende Umgang mit unseren natürlichen Rohstoffen ist ein wichtiger Beitrag zum Umweltschutz und zur Zukunftssicherung nachfolgender Generationen.
Recycling
Recycling-Gesteinskörnung
Recycling-Gesteinskörnung aus Betonbruch hat sich als grobe Körnung in Beton oder als ungebundene Schüttung im Straßenbau bewährt und ersetzt dort Primärrohstoffe. Im Jahr 2018 lag die Verwertungsquote von Betonbruch bei über 90 Prozent (Quelle: www.kreislaufwirtschaft-bau.de, aufgerufen am 28.11.2023). Um den Stoffkreislauf besser zu steuern und zu verlagern, bedarf es jedoch unter anderem gesetzlicher Regelungen und einer vergaberechtlichen Akzeptanz. Diese sollten den Einsatz von Recycling- Gesteinskörnung fördern und Anreize dafür schaffen, einen internen Stoffkreislauf zu integrieren.
Ebenso bedarf es einer deutlichen Vereinfachung bei der Genehmigung von Aufbereitungsanlagen. Durch Recycling-Gesteinskörnung können erhebliche Mengen natürlicher Rohstoffe eingespart werden. Somit stellt das Material eine ökologisch wertvolle Alternative zu natürlichen Rohstoffen dar. Im Hinblick auf die Reduzierung schädlicher Umweltwirkungen ist der Einsatz von Recycling-Gesteinskörnung umso bedeutsamer, je kürzer zum Beispiel ihre Transportwege sind.
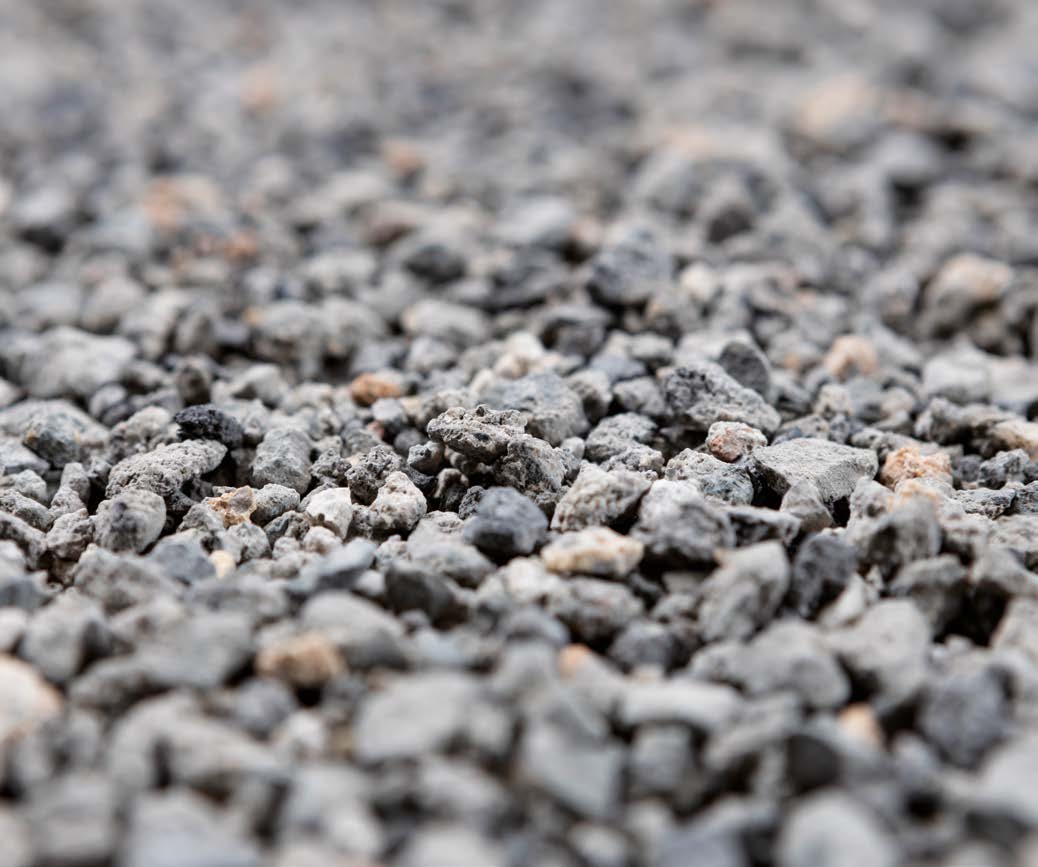
Recycling-Betonpflastersteine
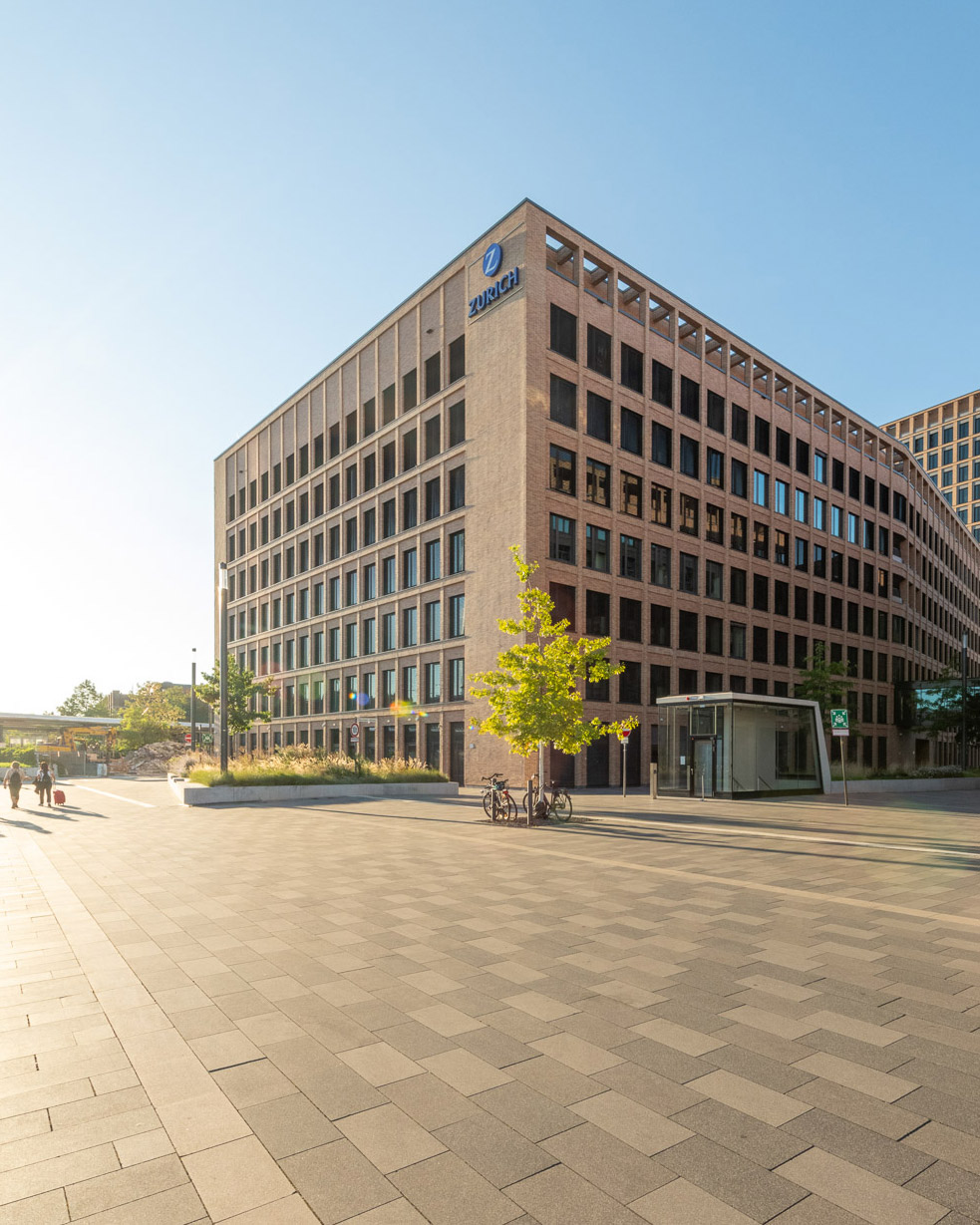
Bereits in den 1990er-Jahren wurden Betonsteinprodukte für die Flächenbefestigung unter Zugabe von aufbereitetem Betonbruch erfolgreich hergestellt und vertrieben. Heute verfügt die überwiegende Anzahl der Betonsteinwerke über geschlossene Stoffkreisläufe, sodass im Zuge der Qualitätskontrolle aussortierte Betonwaren und Fehlchargen zu Recycling-Gesteinskörnung verarbeitet und dem Produktionsprozess direkt wieder zugeführt werden. Da diese Mengen vergleichsweise gering sind, werden zum Teil auch schon ausgediente Betonwaren zurückgenommen und dann aufbereitet. Betonbruch besteht aus reinen Betonabfällen, die keine weiteren Bauabfälle enthalten und somit nur aus den natürlichen Stoffen bestehen.
Recycling-Gesteinskörnung aus Betonbruch ist daher ideal für die Herstellung neuer Betonsteinprodukte, wie zum Beispiel Pflastersteine. Ein moderner Recycling-Pflasterstein aus Beton besteht heute aus rund 30 bis 40 Prozent Recycling- Gesteinskörnung, es konnten aber auch vereinzelt schon Recyclinganteile von bis zu 70 Prozent realisiert werden. Die Zugabemenge variiert hierbei von Hersteller zu Hersteller und von Produkt zu Produkt. Die technische und optische Qualität von Recycling- Pflastersteinen aus Beton bietet den gewohnt hohen Standard genormter Betonpflastersteine. Das Angebot der Hersteller ist mittlerweile sehr vielfältig. Recycling-Pflastersteine aus Beton werden mit harmonischen Farb- und Materialkombinationen sowie mit besonderen Oberflächenstrukturen angeboten. Für jeden Bedarf und jede Anwendung – sowohl im öffentlichen als auch im privaten Bereich – steht das geeignete Produkt zur Verfügung.
CO2-effiziente Zemente
In Deutschland hat sich in den letzten Jahren ein erfreulicher Fortschritt in Bezug auf die Entwicklung und Implementierung CO2-effizienter Zemente abgezeichnet. Die vielversprechenden Entwicklungen zeigen die zunehmenden Bestrebungen, die Umweltwirkungen zu reduzieren und den Weg für eine nachhaltigere Zukunft zu ebnen. Bei der Herstellung von Zement bzw. seinem Vorprodukt Zementklinker werden große Mengen CO2 freigesetzt. Rund zwei Drittel davon entfallen auf rohstoffbedingte Prozessemissionen aus der Entsäuerung des Kalksteins und rund ein Drittel auf energiebedingte CO2-Emissionen aus dem Einsatz der Brennstoffe. Seit 1990 ist es den Zementherstellern in Deutschland durch die Anwendung fortschrittlicher Herstellungsverfahren und die Integration umweltfreundlicher Technologien gelungen, die CO2- Emissionen in einer Größenordnung von 20 bis 25 Prozent zu reduzieren. Weitere bedeutende Meilensteine in dieser positiven Entwicklung sind die verstärkte Forschung und Innovation im Bereich der CO2-armen Zemente sowie auch die Abscheidung von CO2 im Zementwerk und dessen anschließende Nutzung bzw. Speicherung, dem so genannten Carbon Capture and Utilisation/Storage (CCUS).
Diese innovativen Ansätze tragen nicht nur dazu bei, die Umweltwirkungen zu minimieren, sondern fördern auch die Wettbewerbsfähigkeit der deutschen Zementindustrie auf dem internationalen Markt. Ein vielversprechender Aspekt ist die steigende Akzeptanz und Nachfrage nach so genannten „grünen Zementen“. Diese umweltfreundlichen Zementsorten, die in DIN EN 197-5 und DIN EN 197-6 seit kurzem genormt sind, zeichnen sich durch einen reduzierten CO2-Fußabdruck während der Herstellung aus. Die ambitionierten Ziele und Strategien zur Reduzierung von Treibhausgasemissionen hat die Zementindustrie in ihrer Studie „Dekarbonisierung von Zement und Beton – Minderungspfade und Handlungsstrategien“ aus dem Jahr 2020 dargelegt. Insgesamt lässt sich feststellen, dass die Zementindustrie in Deutschland auf dem richtigen Weg ist, umweltfreundliche und nachhaltige Praktiken zu etablieren. Die positiven Entwicklungen der letzten Jahre, gepaart mit dem klaren Engagement für die Dekarbonisierung bis 2050, schaffen eine optimistische Grundstimmung für eine Zukunft, in der die Zementproduktion zu einer treibenden Kraft für den Klimaschutz wird.